Reflanging machine MRIFL
The explicit purpose of a spool reconditioning unit is to return B-type spools, commonly used for the winding of tire-cord, to their original dimensional tolerances through the restoration of the orthogonality between the flange and the barrel.
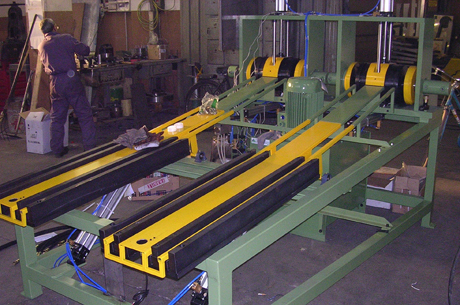
/
Reflanging machine MRIFL
The explicit purpose of a spool reconditioning unit is to return B-type spools, commonly used for the winding of tire-cord, to their original dimensional tolerances through the restoration of the orthogonality between the flange and the barrel. This result is obtained by pressing the flanges by means of hydraulic heads, whose set-up can vary depending on the deformation degree of the flanges.
The reconditioning machine is not suitable for the reparation of damages/deformations on the barrel. The reconditioning cycle of the spools and their control post-pressing is performed in a completely automatic way. Once positioned on an appropriate chute, the spools are automatically driven to the holding cradle. The expulsion of the spool after the cycle is obtained by means of an automatic device which positions the spool on a chute equipped with control guides adjustable by the operator.
The spools needing a further repressing size after the reflanging process are blocked by the machine, automatically removed and stored in a tank where the operator can recover them for a possible further pressing cycle. The reflanging machines MRIFL are highly customizable and are available in the following versions:
Single or double reconditioning line
Depending on the required productivity, the reconditioning machines MRIFL can be supplied with single or double reconditioning line. A double-line reconditioning machine ensures a higher productivity and is able to recondition different models of spools at the same time. Each holding cradle can be equipped to recondition both B40-B60 or B80 spools. It is possible to change the set-up of the machine from B40-B60 to B80 (or vice versa) in a few working hours and without A.Appiani Srl staff intervention (an instruction manual is supplied ).
Partial or complete reconditioning cycle
The following reconditioning typologies are available:
- Simple (partial) reconditioning, which consists in the straightening of the spools with outward deformation of flanges
- Complete reconditioning, which consists in the straightening of the spools with outward and inward deformation of flanges - this last type of deformation is caused usually by falls or crushing.
Linear layout or chutes returning to the operator
Depending on the customer\'s needs, the MRIFL machines can be provided with a linear expulsion chute (linear MRIFL) or, alternatively, with an automatic system for the return of the spools to the operator (MRIFL with return to the operator). This \'return\' device drives the spools to the initial loading position so that even a single operator can unload them from the machine, with consequent benefits in terms of productivity. In the case of MRIFL with linear expulsion chute the presence of 2 operators is necessary, one for the loading of the spools on the machine and the other one for unloading and packaging.
AVAILABLE REFLANGING MACHINES
DIMENSIONS | TYPE OF RECONDITIONING | LAYOUT | QUANTITY OF RECORDING HEADS | MAX ESTIMATED PRODUCTIVITY | DIMENSIONS | |
---|---|---|---|---|---|---|
1 | RIF1T | STANDARD | LINEAR | SINGLE | 250 PIECES/HOUR | 10mx2m |
2 | RIF1T | COMPLETE | LINEAR | SINGLE | 250 PIECES/HOUR | 11mx2m |
3 | RIF1T | STANDARD | RETURN TO OPERATOR | SINGLE | 280 PIECES/HOUR | 9mx3m |
4 | RIF1T | COMPLETE | RETURN TO OPERATOR | SINGLE | 280 PIECES/HOUR | 10mx3m |
5 | RIF2T | STANDARD | LINEAR | DOUBLE | 600 PIECES/HOUR | 10mx3m |
6 | RIF2T | COMPLETE | LINEAR | DOUBLE | 600 PIECES/HOUR | 10mx3,5m |
7 | RIF2T | STANDARD | RETURN TO OPERATOR | DOUBLE | 650 PIECES/HOUR | 9mx5m |
8 | RIF2T | COMPLETE | RETURN TO OPERATOR | DOUBLE | 650 PIECES/HOUR | 10mx5m |
• The theoretical time of completion of the cycle is 7 seconds (each reconditioning head)). The estimated maximum productivity indicated in the table above includes possible arrests related to logistics operations
• The dimensions listed above are non-binding standards. The length of loading and unloading chutes is at the discretion of the customer and can be modulated as per request
• In addition to the electrical connection, the machine needs a limited amount of compressed air
• Protective barriers are provided for use in accordance with the accident prevention norms
• CE certification according to current standards and use and maintenance manual are supplied
• Electrical set-up and PLC carried out according to EU standards
• The fixing of the machine to the ground is accomplished without need for foundations
• Epoxy painting as per customer request (all RAL colors available)
If you need more information about the technical specifications and the supply conditions of the machine please contact A.Appiani Srl.
/
GALLERY
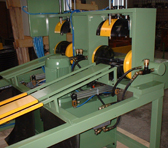
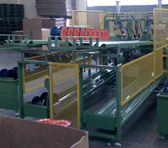
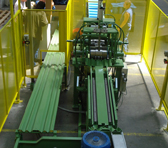
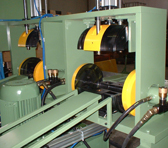
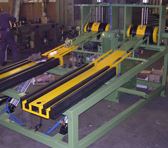
This product doens't have a dimensional sheet.